Kinh Nghiệm về Which of the following is reason operations managers need project life-cycle management (plm) tools? Mới Nhất
Hoàng Gia Trọng Phúc đang tìm kiếm từ khóa Which of the following is reason operations managers need project life-cycle management (plm) tools? được Update vào lúc : 2022-09-04 07:48:02 . Với phương châm chia sẻ Bí kíp Hướng dẫn trong nội dung bài viết một cách Chi Tiết Mới Nhất. Nếu sau khi tham khảo tài liệu vẫn ko hiểu thì hoàn toàn có thể lại Comment ở cuối bài để Admin lý giải và hướng dẫn lại nha.Product life cycle management is the process of managing the entire life cycle of a product from inception, through engineering design and manufacture, to service and disposal of manufactured products.
Nội dung chính- Product and plant knowledge management7.2.1 Product life cycle managementDetailed Design8.7.1 Product Life Cycles and Environmental ImpactsCircular materials—An essay on challenges with current manufacturing and recycling strategies as well as on the potential of life cycle integrated designs1 IntroductionSustainable apparel retail8.4 Retail impactsManufacturing Engineering Requirements in the Early Stages of New Product Development—A Case Study in Two Assembly Plants5.1 IntroductionIntroduction of medical devices1.5 Product life cycle of medical deviceProduct Data Management6.4.2.2 Arena Cloud PLMReframing Product Life Cycle for Medical DevicesEnvironmental impact of architectural fabric structures10.4 Environmental product declarations (EPD)The “Material” Side of Design for SustainabilityThe product life cycle phases
From: Production Planning and Control, 2022
Product and plant knowledge management
In Practical E-Manufacturing and Supply Chain Management, 2004
7.2.1 Product life cycle management
Product life cycle management (PLM) is a comprehensive and integrated suite of software solutions designed to support optimal decision-making during product development. It is the only market solution that uses advanced planning and optimization tools to address the entire product life cycle – from concept development, to launch, to phase out. Product life cycle management maximizes the speed, productivity and the financial return of the product development process.
Product life cycle management is part of a total strategy to achieve effective and more profitable manufacturing. Manufacturing operations need PLM systems that manage product specifications and recipes, provide production history, create complete product genealogies and track total product quality.
Product life cycle management addresses effectively selected and managed product development investments and resources, in order to ensure rapid product development speed, high development throughput and high organization efficiency. Product platforms, parts, and suppliers for lowest total product and supply-chain cost are to be defined, based on optimal commonality and effective part/supplier selection.
Key development and supply activities are coordinated for optimal product launch-timing and investments in new/existing products. This enables the achievement of consistent high-product launch yields, with reduced product development lead-times. It provides enhanced visibility of resource bottlenecks and schedule impact whilst avoiding high part and supplier complexity with too little commonality, and budget over-runs.
The emergence of creative solutions that solve customer problems and reduce costs requires a rich exchange of information and ideas. Virtual collaboration and PLM technologies increase the variety and frequency of information exchanged throughout the design team to enable creative decision-making. Virtual collaboration technologies are a subset of PLM and include visualization and simulation tools as well as one-to-one scale graphics displays and conferencing. These technologies improve understanding of product designs by allowing teams to jointly interact with a visual model.
Comprising much functionality, including collaborative engineering, sourcing for direct materials, and project and program management, PLM is one of the great emerging territories in B2B technology. Born as an extension of product data management (PDM), the PLM space has huge potential because of the value it offers to manufacturers that master it.
Read full chapter
URL: https://www.sciencedirect.com/science/article/pii/B9780750662727500105
Detailed Design
Joseph Tranquillo PhD, ... Robert Allen PhD, PE, in Biomedical Engineering Design, 2023
8.7.1 Product Life Cycles and Environmental Impacts
Product life cycles typically last for months to years depending on the product. They start with extraction and processing of raw materials from natural resources. These raw materials are then used to manufacture the product, after which the product is distributed and used. When the product is no longer useful, it might be remanufactured, components might be reused, materials might be recycled, or the product might be disposed of by incineration or deposition in a landfill. Each of these stages in the product life cycle may consume energy and generate emissions and waste, resulting in environmental impacts. These impacts include liquid discharges, gaseous emissions, energy consumption, depletion of nonrenewable natural resources (such as helium and metals), and generation of solid waste. Discharges, emissions, and solid waste may be comprised of toxic substances that can poison or damage the environment and contribute to pollution of air, soil, and water, as well as land degradation and ozone depletion. Products that release relatively large amounts of carbon-based gases (such as carbon dioxide and methane) into the atmosphere have large carbon footprints, which contribute to climate change.
Read full chapter
URL: https://www.sciencedirect.com/science/article/pii/B9780128164440000080
Circular materials—An essay on challenges with current manufacturing and recycling strategies as well as on the potential of life cycle integrated designs
Ludovic F. Dumée, in Circular Economy and Sustainability, 2022
1 Introduction
Product life cycle as commonly accepted over the course of a linear economy (LE) is the set of identified stages in the life of commercial products (Rink and Swan, 1979). These stages include (i) development, (ii) introduction, and (iii) growth, as well as (iv) maturity, (v) decline, and (iv) disposal (Blythe, 2009). Market research and competitor analysis are obviously the main part of the development stage, which are performed to get an idea of the potential growth for the product and to build a business case to validate the products. During the introduction phase, the product is initially promoted to develop public awareness about the upcoming product. This marketing exercise spans across a range of truyền thông and diffusion mechanisms to promote the key criteria of interest to the customer: the performance of the product. The growth stage occurs when the market share of the product becomes visible above the noise of its competitors. If a product completes the introduction and growth stages, it will progressively reach the maturity stage. During this maturity stage, typically the longest over the lifetime of a product, dissemination of the product grows a very fast rate, prior to gradually plateauing. The key for a product to overcoming risks of market obsolescence and decline is achieved through differentiating the product from its competitors or by upgrading the product further to account for customer feedback. At the end of its lifetime, the product may be disposed of and may be recycled, if considered cost-effective, or sent to landfill or for incineration. The innovation in terms of performance of the product will dictate when the product enters its decline stage, leading to a reduced market share and ultimately, an end of production. This model has thrived for over 100 years since the inception of mass production as the leading model of our economies.
This linear economy model, therefore, encompasses several design and redesign steps allowing for market penetration, adaptation to competitors and needs or demand from customers about performance (Sariatli, 2022). Circular design is just one extra performance criteria demanded by customers to ensure that the end of life of their products is not only predicted and controlled but sustainable. This demand, driven by environmental concerns and an increased awareness of mankind's responsibility for the abuse of natural resource and their management, will lead markets and force manufacturers to develop innovative solutions to loop their materials development (Garcés-Ayerbe et al., 2022; Jørgensen and Pedersen, 2022).
Despite often being considered a brake to competitiveness in terms of profit, redesigning materials for a circular economy does not necessarily require extensive alteration to initial designs (Moreno et al., 2022). Examples of competitor products on the market allowing for easy disassembly leading to the recovery of parts which can be readily recycled or else repurposed are common. In parallel, the use of various materials grades allowing for cost-competitive recycling strategies has often hindered the development of circular recycling pathways due to the mismatch of the various grades of materials recovered within recycling stations (Sariatli, 2022). The economy of scale achieved by reducing or altering the quality of raw products used may indeed affect the ability to recover materials and render recycling efforts vain or inefficient (Garcés-Ayerbe et al., 2022).
In this chapter, the origin of barriers preventing strategies to the development of a circular design of materials will be discussed (Kirchherr et al., 2022). A strong focus will be put on the rationalization of materials and on better awareness of the source and finite nature of the resources used for product manufacturing, as well as to the design of the system to facilitate recovery of components and individual materials (Savini, 2022). Considerations related to advanced recycling solutions of products will also be discussed in light of needs to close the loop. It is urgent to shift, the corporate, governmental, and consumer levels, the concept of waste to resource. Currently, by labelling end-of-life products as waste, the value and potential of these materials is immediately diminished, leading regulatory bodies to handle them as nonvaluable materials (Group et al., 2022). A paradigm both from a societal and industrial point of view must be reached whereby such products, representing resources, are redefined to be intelligible to the various stakeholders of the design, manufacturing, and recycling chains. The objectives of any circular economy approach are to enhance the lifetime of products, facilitate repurposing of items, and divert waste materials from landfill back to production lines. In the long term, such approaches may be achieved through rationale design of products, which may be easily dismantled into core parts for repurposing or recycling. However, in the short term, redefining wastes as resources to optimize their recovery is a key priority.
This chapter aims acting both as a critical review and an opinion. It will first present the barriers and enablers of circular design to identify recurring challenges preventing its implementation. Then it will focus on the various current classes of materials resources and highlight flaws in their designs preventing their facile repurposing or recycling. Last, it will discuss strategic routes to favor a circular design approach.
Read full chapter
URL: https://www.sciencedirect.com/science/article/pii/B978012821664400008X
Sustainable apparel retail
M.P. Sumner, in Sustainable Apparel, 2015
8.4 Retail impacts
The sustainability challenges facing a retailer are not limited to a retailer’s operational impacts. As discussed, the majority of these sustainability challenges are associated with their products and their supply chains. But other impacts are associated with the product after it has been purchased by the consumer. It is now common to consider the sustainability of a retailer in a much wider context that reflects the life cycle of their products.
The product life cycle considers not just the impacts created through the sourcing of materials, the manufacturing process, and the impacts associated with retail operations such as logistics and warehousing, it also incorporates the “use” phase of products and the impact of the disposal of the product the end of its life. Figure 8.2 is an example of a product life cycle, and it is a representation of the energy use for each of the key stages of a typical apparel product:
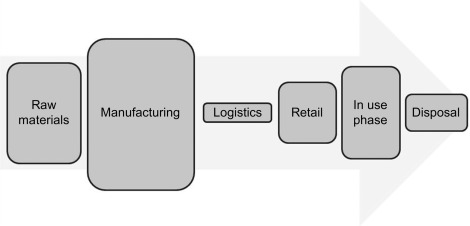
Figure 8.2. A representation of energy use across a product life cycle.
●Raw materials: Energy use to extract or grow the raw materials. For polyester this could include the energy required to extract and refine the crude oil used to produce ethylene, one of the base molecules for polyester fiber. Or it could include the energy consumption for the production of nitrogen fertilizers used in cotton cultivation.
●Manufacturing: Consumption of energy for textile processes such as ginning, spinning, weaving, dyeing, and garment production.
●Logistics: Related to the energy needed to transport the finished goods from the manufacturer to the retailer.
●Retail operations: Energy consumption by the head office, warehouses, stores, and local logistics functions of the retailer.
●Use phase: For clothing this generally refers to the energy consumption for washing, drying, and ironing.
●Disposal: The energy balance for this stage is determined by the disposal option used, which can include reuse, recycling, incineration, or disposal to a landfill. In the case of incinerated garments there could be a potential positive impact in terms of energy production if incineration is part of an energy recovery system.
In general, the magnitude of impacts associated with raw materials, the manufacturing processing, and logistics are controlled by suppliers, whereas the scale of impacts attributed to the use phase and disposal are determined by the consumer. The retailer has direct control of the energy impacts associated with the retail operations, assuming they own the stores and they are not operating a concession or franchise model.
By using this type of analysis, retailers and others have been able to show the life-cycle impacts for various products and from this, hot spots or points of significant impact within the life cycle have to be identified. Hot spot analysis is an important way to identify where retailers should make their investments to maximize the results. For example, consider Figure 8.3, which is a representation of the typical water-consumption impacts for a clothing product. From this we can see that a significant proportion of the water consumption is associated with the raw materials and the manufacturing process. Some retailer analysis has shown these two stages of the life cycle represent up to 99% of the water impact. If a retailer does not perform this type of “hot spot” analysis, the retailer may spend thousands of dollars on water-saving devices within the “retail” stage of the life cycle but only be able to influence just 1% of the overall water use. Through analysis of the product life cycle and identifying hot spots it would be better to consider investments in water-saving strategies for the supply chain where there is a much larger opportunity to save water.

Figure 8.3. A representation of water use across a product life cycle.
Figures 8.2 and 8.3 are simple representations of a single sustainability impact or dimension, in this case, energy use and water use. But there are a multitude of different impacts categories, such as green gas emissions, toxicological loading, eutrophication, land use, and more that need to be considered to fully evaluate the sustainability of a retailer. Hot spot analysis can be used to assess impacts for a large number of sustainability categories for individual products and for the whole of the retailer’s portfolio of operations. However, whether the analysis is done a product level or organizational level, a deep understanding of the life cycle is required.
As an example of the detail needed to create a useful life-cycle analysis, consider the water footprint for a cotton T-shirt. For this T-shirt, the supplier has the choice of using cotton fiber grown in either India or Australia. The Australian cotton has a water footprint of 2278 m3 per ton of fiber. Cotton grown in India, however, has a water footprint of 8662 m3 per ton of fiber. This represents a fourfold increase in water impact the raw material stage of the life cycle simply as a result of changing the source of the cotton. Another hot spot for water use in the supply chain is the coloration of the fabric. The complexity of information required to determine water use during coloration is demonstrated in Figure 8.4, which shows the basic processes for the coloration of a cotton fabric. Not only are there a number of different process that need to be assessed in terms of water footprint, there are a multitude of machine types and chemicals that can be used to pretreat, dye, and finish fabrics. Pretreatment processes using enzymes can minimize water use; the latest dyeing machines are significantly more water efficient as compared to older machines, whereas new dyestuffs require less washing off, which leads to water savings. The granularity of data needed to assess the impacts of these different processes, machinery, and chemicals is significant.

Figure 8.4. A typical dyeing and finishing process for cotton.
The third hot spot for water consumption is the “use” phase of the life cycle. The magnitude of water use this stage is determined by the number of times the consumer washed the product. For a retailer to establish the full life-cycle water footprint of one cotton T-shirt he or she would need to know where the cotton was grown, the chemicals, processes, and equipment used in the dyeing process and how many times the consumer washed the product; considerable knowledge about the extended supply chain and consumer behavior is needed to complete the analysis. The complexity of the assessment process is even more challenging when the social and ethical aspects of sustainability are considered. What level of data granularity is required to understand the social standards of one factory compared to another, or how the animal welfare standards for sheep farming in Australia compared to sheep farming in South Africa? And for the coloration example, the social dimensions such as working conditions, exposure to harmful chemicals and labor rights would need to be assessed for the workers and the community surrounding the dyehouse.
These are challenging questions for retailers, and this level of data can only be sourced from the supply chain. It is clear that a key component to developing solutions to the sustainability challenges the industry is facing lies with the relationships and understanding retailers have of their extended supply chain.
Read full chapter
URL: https://www.sciencedirect.com/science/article/pii/B978178242339300008X
Manufacturing Engineering Requirements in the Early Stages of New Product Development—A Case Study in Two Assembly Plants
Mariam Nafisi, ... Anna Granlund, in Advanced Applications in Manufacturing Enginering, 2022
5.1 Introduction
As product life cycles get shorter and customer demands become more diverse, manufacturing companies are pressed to release new products onto the market faster and more frequently [1]. Therefore new product development (NPD) is crucial for the survival and prosperity of companies in different sectors, whether they offer products or services [2,3].
New products need to be superior to their predecessors in terms of quality, function, features, and price [4]. Manufacturing enterprises should integrate their innovative products with their manufacturing system capabilities [5]. A mismatch between the product design and manufacturing process capabilities makes it impossible for the company to manufacture a high-quality product cost effectively. In practice, this misalignment leads to an unavoidable increase in manufacturing costs and to launch delays. Therefore it is important to take manufacturing and assembly into account as early as possible during product design [6]. To reduce time to volume and to improve coordination between design and manufacturing, product development and manufacturing development activities should be carried out in parallel and should be integrated [7]. The integration of design engineering and the manufacturing process ensures a reliable product without defects [8]. Several concepts are introduced to enable integration, including but not limited to concurrent engineering (CE), integrated design and engineering, and design for manufacturing/design for assembly (DFM/DFA) [9].
The success of a new product in the market relies on the success of its respective development project. Therefore NPD projects are of high importance for companies and take up a lot of resources and budgetary funds. Despite all the effort that companies put into their NPD projects, many new products fail for different reasons [2,10] and do not meet their financial objectives or launch dates.
NPD projects vary in their content, purpose, and extent, and every project has unique characteristics and different challenges. However, a common characteristic of NPD projects is that they are information-intensive [11]. NPD projects require collaboration and information exchange the right time. Various functions are involved in the activities each project stage, which necessitates cross-functional contact and communication.
One important aspect of NPD projects is the interface between manufacturing and product development functions. Historically, manufacturing has had less stature than other functions involved in NPD, even though manufacturing involvement in NPD activities has been shown to have advantages [12]. It is important that manufacturing system capabilities, limitations, and requirements are communicated to the product design team early in the NPD project to minimize design rework and extra cost. Manufacturing has the knowledge and expertise that is required to move from product innovation to mass production [12]. While limitations in a manufacturing system should not hinder innovativeness in new products, manufacturing capabilities, limitations, potentials, and goals should be considered when new products are being planned and designed [13,14]. Manufacturing can provide product design teams with input about what is feasible and what is not [12]. As indicated in previous studies, the link between product design and manufacturing should be established early in the NPD project to ensure that interdependencies among them are recognized and resolved [8,15]. Problems that are discovered late (e.g., during detailed design or manufacturing) are costly to fix [14].
Tackling this issue requires effective design–manufacturing integration and communication early in the NPD process. This is to ensure that manufacturing requirements are communicated to product design teams to avoid design rework and achieve better product fit for the manufacturing system.
Many integration mechanisms are discussed in the literature, with the focus being on integration management, enablers, and barriers [16–18]. While providing useful insight regarding integration, many of these mechanisms remain a general project level, and there are no practical guidelines about integrating manufacturing requirements in NPD activities. In addition, there is little research addressing manufacturing involvement in the fuzzy front end of NPD with respect to challenges and proper integration mechanisms.
Therefore the purpose of this chapter is to investigate types of manufacturing requirements and how these requirements are integrated into the fuzzy front end of NPD projects when an existing manufacturing system is to produce the new product. We begin with mapping and analyzing manufacturing requirements in two industrial cases for this type of NPD project. We then investigate what mechanisms are used to communicate and integrate these requirements. The chapter concludes by reflecting on the suitability/efficiency of these mechanisms for defining, communicating, and following up various kinds of requirements throughout NPD projects.
Read full chapter
URL: https://www.sciencedirect.com/science/article/pii/B9780081024140000057
Introduction of medical devices
Aakash Deep, in Medical Device Regulations, 2022
1.5 Product life cycle of medical device
The Medical Product Life Cycle is associated with regulatory processes for industry leaders in the United States, the European Union, and other countries that mimic their policies. However, the relationship between the Legislative Council and regulation is not always clear to many. Managing products throughout their lifecycle is essential for end users, and thus for the companies that produce and market them.
Understanding the inseparable link between regulation and markets and therefore the medical device industry is essential for the assembly of safe and effective devices, sustainable clinical improvements for the industry, and thus for long-term medical ethics dates “do not hurt” [11].
Read full chapter
URL: https://www.sciencedirect.com/science/article/pii/B9780323911269000018
Product Data Management
Kuang-Hua Chang, in e-Design, 2015
6.4.2.2 Arena Cloud PLM
Arena pioneered cloud PLM applications. The company's products, including BOMControl, PartsList, and PDXViewer, enable engineering and manufacturing teams and their extended supply chains to speed up prototyping, reduce scrap, and streamline supply chain management. Arena cloud PLM applications simplify the BOMs and change management for companies of all sizes, and they offer the right balance of flexibility and control every point in the product lifecycle—from prototype to full-scale production. These cloud-based applications enable manufacturers to manage BOMs, engineering change orders, product data exchange (PDX), and other key manufacturing files securely and efficiently.
PLM in the cloud is an internet-based system for managing a product and its associated information from concept to end of life. PLM in the cloud is growing in popularity with manufacturers around the world as a way to manage the stages of product development in order to collaborate, track, and regulate changes to the product. BOMControl (see Figure 6.14) keeps BOM data centralized, controlled, and up-to-date, resulting in fewer errors, less scrap and rework, higher quality, and better cost control.

Figure 6.14. Sample screen shots of Arena cloud product life cycle management (en.wikipedia.org/wiki/ProductCenter).
Read full chapter
URL: https://www.sciencedirect.com/science/article/pii/B9780123820389000065
Reframing Product Life Cycle for Medical Devices
B.A. Fiedler, Y. David, in Managing Medical Devices Within a Regulatory Framework, 2022
Abstract
The medical device product life cycle (PLC) is linked to the regulatory processes in industry leaders in the United States, European Union and other countries who emulate their policies. Still, the link between PLC and regulation is not always clear to many. Product management through its life cycle is critical to end users and the companies that produce and market them. Understanding the inseparable link between regulation, markets, and the medical device industry is critical to the production of safe and effective devices, industry sustainable, clinical improvements, and the long-standing medical ethical position of ‘do no harm’.
Read full chapter
URL: https://www.sciencedirect.com/science/article/pii/B9780128041796000010
Environmental impact of architectural fabric structures
J.M. Cremers, in Fabric Structures in Architecture, 2015
10.4 Environmental product declarations (EPD)
Drafting a product LCA is a time-consuming and expensive process that is generally carried out for the product manufacturer or a group of manufacturers by a specialist company. The ecological characteristics of a product are communicated in the form of environmental declarations. According to the ISO 14020 family, these environmental product declarations (EPD) are classified as so-called type III environmental labels, which are highly regulated. Here, the most important environmental impacts of products are described systematically and in detail. The starting point is a product LCA, but further indicators specific to the product (e.g. contamination of the interior air) are also included. In this form of declaration, it is not the individual results of measurements that are checked by independent institutes, but rather conformity with the product category rules (PCR) drawn up to ensure an equivalent description within that product category. An EPD describes a product throughout its entire life cycle – all relevant environmental information. They are third-party verified and guarantee reliability of the information provided. Calculation rules for EPDs are defined by EPD program holders – for building products, EN 15804 is introduced as the respective standard in Europe.
EPDs help in the early planning stage. They show environmental performance of a product or a product group; they are often used in political discussion and can be a basis for a company's internal benchmark and improvement.
Figure 10.9 shows the different stages addressed by different types of EPDs (product, manufacturing/construction process, use, end-of-life and potential effects beyond the system boundary).

Figure 10.9. EPD framework – EN 15804 (system boundary and modularity of product life cycle). Types of EPD with respect to life cycle stages covered and life cycle stages and modules for the building assessment.
PE International.Read full chapter
URL: https://www.sciencedirect.com/science/article/pii/B9781782422334000103
The “Material” Side of Design for Sustainability
Carlo Vezzoli, in Materials Experience, 2014
The product life cycle phases
Assuming a product life cycle approach means to consider any effects with the biosphere and geosphere determined by all the inputs and outputs of all the processes associated with a given product. Usually five life cycle phases are identified (although all the processes related to all the life cycle phases are considered simultaneously as a single unit):
•preproduction, encompasses the raw material/resources/supplies acquisition, and refinement processes;
•production, the processing, assembling, and finishing phases;
•distribution, packing, transport, and storage;
•use of the product, including consumption of the resources required for its operation, if applicable, and connected processes like maintenance;
•disposal of the product, which may follow a number of different paths after its re-collection: landfill, incinerator, conversion into compost, recycling, remanufacturing, or reuse (of the entire product or some of its parts).
Read full chapter
URL: https://www.sciencedirect.com/science/article/pii/B9780080993591000084
Tải thêm tài liệu liên quan đến nội dung bài viết Which of the following is reason operations managers need project life-cycle management (plm) tools?