Mẹo Hướng dẫn What is the total cost approach to logistics? Mới Nhất
Dương Gia Minh đang tìm kiếm từ khóa What is the total cost approach to logistics? được Update vào lúc : 2022-11-24 08:22:21 . Với phương châm chia sẻ Mẹo Hướng dẫn trong nội dung bài viết một cách Chi Tiết 2022. Nếu sau khi đọc nội dung bài viết vẫn ko hiểu thì hoàn toàn có thể lại Comment ở cuối bài để Ad lý giải và hướng dẫn lại nha.CapabilitiesTotal Cost Approach Nội dung chính Show
- Total Cost Approach How it WorksWhat Are Logistics Costs?4 Main Types of Logistics CostsWarehousing and inventoryTransport and distributionEquipment and suppliesHow to Measure Logistics Costs4 Strategies for Reducing Logistics CostsBring delivery in-houseLeverage software to streamline last mile deliveryOptimize inventory levelsAudit warehouse and inventory management processesOptimize Your Logistics Operations With OptimoRouteFAQs About Logistics CostsWhat is the biggest logistic cost?How do you calculate logistics costs?Why is logistics so expensive? Try OptimoRoute™ for FreeWhat are the total logistics cost factors?What is total system approach to marketing logistics?Why is the total cost of logistics model important?What is total cost concept in supply chain management?
Total Cost Approach
How it Works

By optimizing the packaging design to the supply chain, Nefab can reduce the overall transport costs for you. With tailored packaging solutions, you can fit more products into each shipment, container and truck, and thereby save money on shipping costs.

A packaging solution should enable a safe, easy and fast packing and loading procedure. With improved working environment and reduced handling time, you can focus on your core processes rather than packing and packaging.

With our complete packaging solutions offer, JIT-deliveries and Vendor Managed Inventory (VMI) services, you can enjoy improved delivery planning and turn fixed costs into variable. At the same time, working capital can be reduced as well.

On its way in transit, the packaging protects the goods from stresses throughout the supply chain. It is easy to build a strong packaging that will do the job, but the ingenious solution is the one that do the job with the minimum level of material, thus optimizing the cost for packaging, damages and claims.

By designing collapsible packaging solutions with optimal fill factor and stacking capability, Nefab enables you to save space in the receiving area as well as in the warehouse, for finished goods.

The choice of packaging material will impact waste management and the costs for waste disposal, which should be considered as part of the total cost for a packaging solution. Moreover, Nefab designs packaging solutions that reduce the overall environmental impact in production, transport and end of life treatment.
May 2, 2022
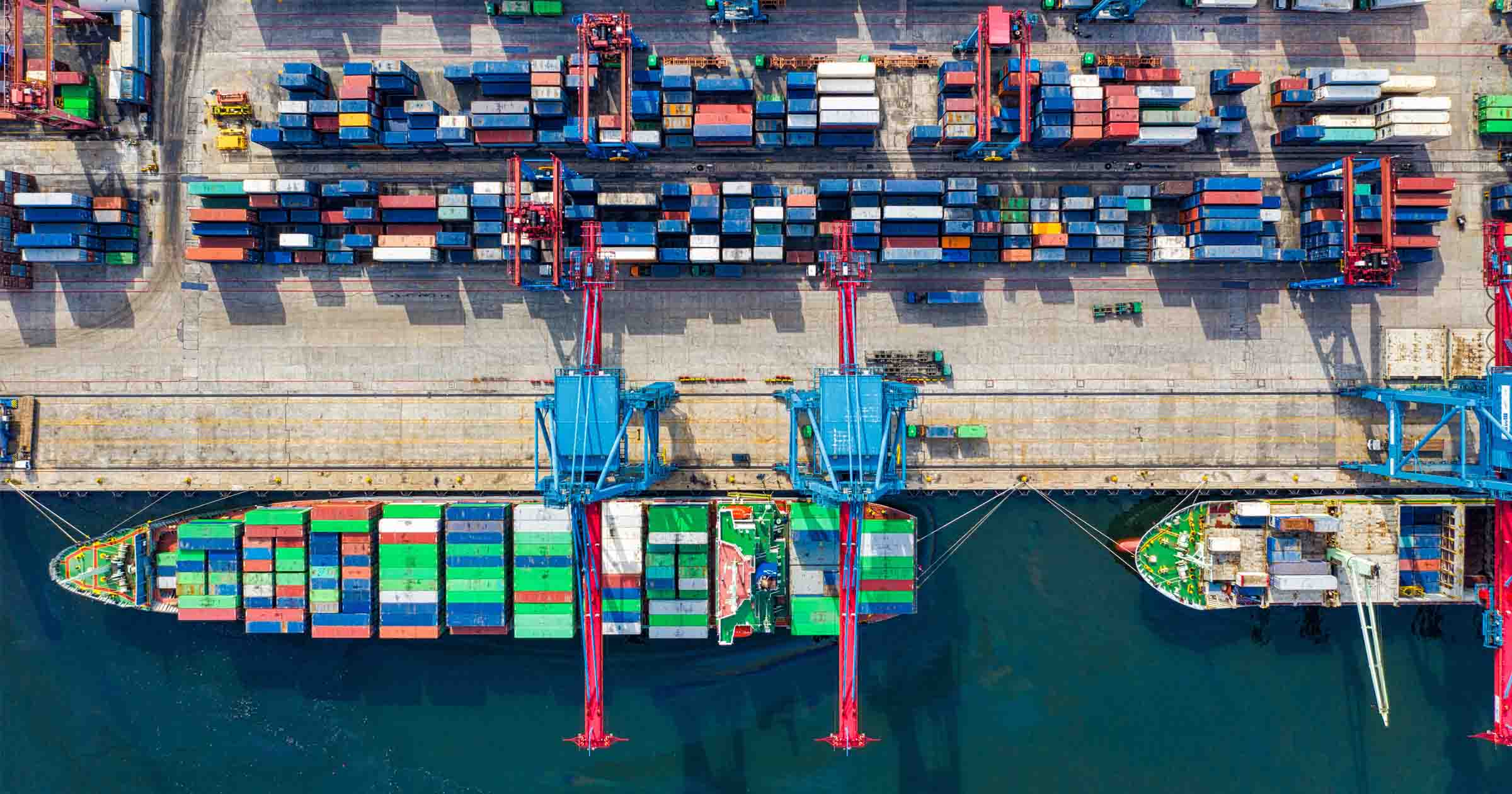
Shipping and logistics costs have been on the rise since the start of the COVID-19 pandemic—and prices will continue to rise across the logistics industry in 2022. These rising costs will have a profound impact on your business. Understanding what logistics costs are will help you classify and measure them for your own business. Then you can identify ways to lower costs and improve your bottom line.
Jump to the section that you’re most interested in:
- What Are Logistics Costs?4 Main Types of Logistics CostsHow to Measure Logistics Costs4 Strategies for Reducing Logistics CostsOptimize Your Logistics Operations With OptimoRouteFAQs About Logistics Costs
What Are Logistics Costs?
Shipping logistics is the process that involves handling, managing, and transporting goods. The term “logistics costs” encompasses all of the expenses associated with this process. Your overall logistics costs include everything from purchasing raw materials to paying a third-party logistics company to help facilitate distribution.
4 Main Types of Logistics Costs
There are many moving pieces within the supply chain. As a result, there is a wide variety of costs associated with logistics management. The specific costs may vary depending on your business and industry, but generally, you can group costs into four different categories: warehousing, transportation, labor, and equipment.
Warehousing and inventory
You need a place to store your inventory, whether you create your own products in-house or rely on a third-party manufacturer. And the larger your inventory is, the larger the space you’ll need. Unfortunately, rising warehousing costs and limited availability make finding a rental space more difficult than ever before. Rental renewals across the United States increased by an average of 25% this year as the growing number of ecommerce businesses creates a shortage of available warehouse space. To avoid this, you could purchase your own warehouse space outright, but it likely won’t be cheaper.
Renting or buying a warehouse isn’t the only cost that fits in this category—you’ll also need to account for other costs like:
- InsuranceUtilitiesSecurity
Transport and distribution
Whether you use third-party logistics service providers (3PL) like a reverse logistics company or rely on an in-house team, transportation and distribution are the largest logistics costs for all businesses. These costs include a variety of tasks, including:
- Transporting raw materials to your manufacturing baseMoving products from manufacturing to your warehouseDelivering packages to customers
Inbound logistics, such as transporting products from the manufacturer to your warehouse, are cost-effective transportation tasks that involve moving large shipments to a single location. However, outbound logistics, such as last-mile delivery, are much more expensive.
Last mile delivery“Last mile delivery” refers to delivering products directly to your customers. It is typically the final stage of distribution. These deliveries take up the most time and resources because drivers must make many stops to deliver small quantities of product to customers. Drivers may face security gates or reception desks that each have a unique process for reception, which can slow down deliveries even more. This makes last mile delivery the largest expense in your supply chain, accounting for half of the total cost of shipping.
Labor
The staff that produces, manages, and transports your products is a logistics cost that can vary greatly. But exactly how much you’ll spend depends on where your staff is located and what the average rate of pay in that area is. For example, if you operate in Texas, then you can expect to pay delivery drivers the local average of $15/hour. But if your deliveries take place in Tp New York City, then you’ll need to pay drivers slightly more to compete with the average pay in the area, which is closer to $20/hour. You’ll also pay team members different wages depending on their job title and level of experience. The specific positions you hire for may vary depending on your business and industry, but you’ll likely need:
- Warehouse staff to receive new inventory and prepare packages for
deliveryDelivery drivers to transport materials and productsManagers to oversee employees as well as warehouse operations and logistics processesAdministrators to manage human resources, including processing payroll, and hiring new employees
Equipment and supplies

The equipment and supplies you need to keep your operations running smoothly also impact your bottom line. This category of expenses encapsulates the cost of a wide variety of items from all aspects of your supply chain. If you manufacture your own products, all of the tools you use for manufacturing will fit into this expense category. Within your warehouse, some of the equipment you may need includes:
- ShelvingPalletsForkliftsBoxesTapeInventory software
For in-house delivery and transportation teams, your equipment costs will also include maps, routing software, driver uniforms, and delivery vehicles. There are also recurring costs associated with in-house delivery, including fuel, insurance, and vehicle maintenance.
How to Measure Logistics Costs
Before you start calculating exact costs, you should first determine what timeframe you’d like to assess. It’s a good idea to measure your logistics costs once a month to ensure your costs don’t exceed your budget. You should also look these metrics on a wider scale to inform reports on your overall business performance. You can do this by measuring your costs each quarter, as well as the end of the year.
Once you’ve selected the time frame, you can begin measuring your costs in all four categories: warehousing, transportation, labor, and equipment. To measure your costs:
List all of your expenses as line itemsList the exact cost of each expenseAdd up the line items in each categoryAdd the expenses in each category togetherThis will show you exactly how much your expenses are in each category. You can add the totals for each category together to find your overall costs.
For example, say you spend $1,000 each month in rent for warehouse space, and the utilities for the space cost $600. For that same month, you spent $1,500 to pay your delivery drivers and another $2,000 for your warehouse staff. For this month-long timeframe, your warehousing costs would total $1,600 while your labor costs total $3,500. However, this is only half of the total monthly logistics costs. To find the full costs, you’d also need to account for transportation and equipment costs.
Assessing your logistics costs can benefit your business by:
- Giving you insight into precisely how much you’re spendingDemonstrating exactly what you’re spending money onMaking it easy to identify ways to lower costs
4 Strategies for Reducing Logistics Costs
Effectively lowering costs is an essential part of a good logistics strategy—it becomes even more important as costs continue to rise and inhibit your ability to make a profit.
Bring delivery in-house
Using a 3PL to complete deliveries eliminates the headache of scheduling and routing. But it’s expensive. Outsourcing leaves you the mercy of how the third-party organization runs its business—if a 3PL’s costs rise, so will the price it charges you for services. Using an in-house delivery team allows you to control the costs and find ways to lower them, such as using reverse logistics.
Building your own delivery team comes with costs, including hiring drivers and buying delivery vehicles. But eliminating the middleman means the profits you earn stay within your business.
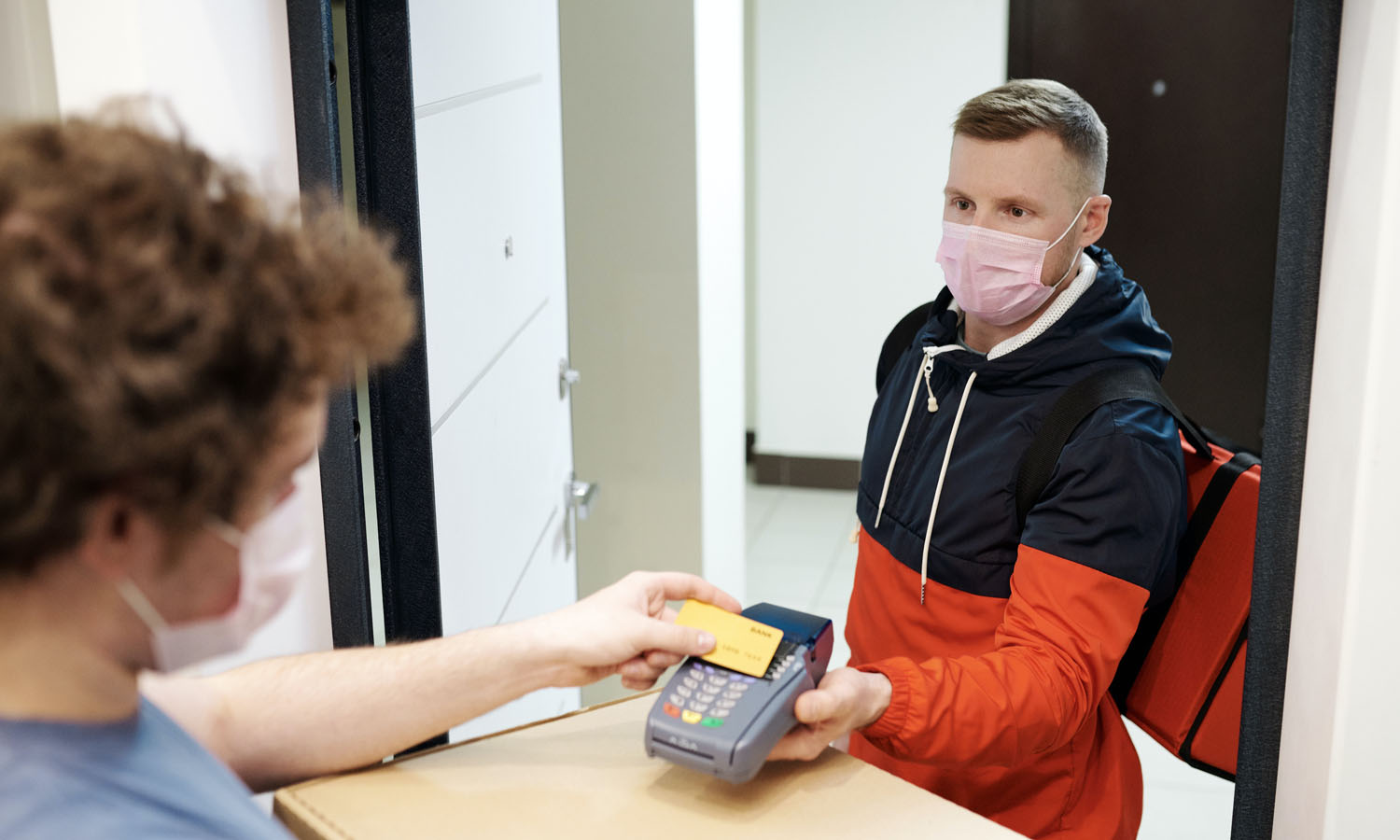
Leverage software to streamline last mile delivery
Last mile delivery is the most expensive aspect of logistics. It’s also the most important phase of delivery because it has the greatest impact on your customers. Despite its importance, planning these deliveries and building the routes for drivers is often a job left to managers or a single dispatcher.
Leaving logistics planning in the hands of a single individual is incredibly time consuming. It also increases the chances of human error, which can lead to late or missed deliveries that will impact your customer’s experience with your business. Using logistics management software streamlines the process by using automation to save time and eliminate errors.
Optimize inventory levels
The smaller your inventory is, the less space you’ll need to house it, and the less you’ll spend on warehousing. But simply reducing the size of your inventory may leave you without the product you need to fill customer orders, leading to delivery delays that can hurt your business’ reputation. Effective inventory optimization will help you determine how much of which products you should keep on hand for optimal inventory levels.
How to optimize your inventory:
Calculate average daily salesMake specific notes about the sales of each productAssess how long it takes shippers to prepare orders for deliveryCalculate how much product you need to meet daily ordersShrink inventory to meet standard daily ordersYou should also keep extra stock on hand (often called safety stock). This will help you make sure an unforeseen problem, like a delayed shipment from your manufacturer, doesn’t impact your ability to fill customer orders.
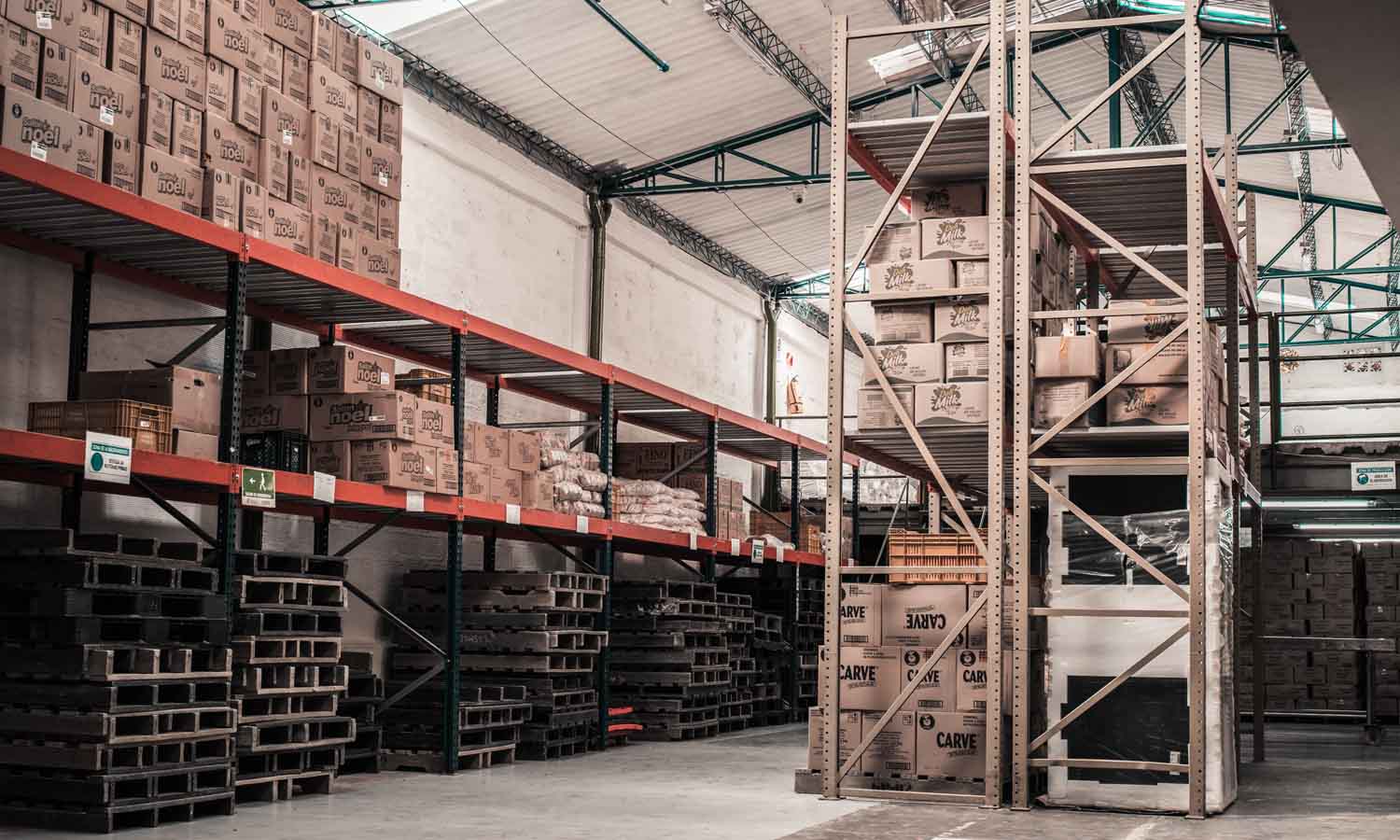
Audit warehouse and inventory management processes
Audits of your warehouse management processes will give you insight into how efficient your workflows are. You should also regularly assess how much product you have on hand for effective inventory management. Conducting these audits regularly (monthly or quarterly) will help you monitor factors that may fluctuate, such as seasonal changes in demand, so that you can adjust your workflows when you need to. There are several different aspects you should assess when auditing your warehouse:
- How your team receives and manages shipments of new productWhere product is stored within the warehouse and how easy it is to accessHow efficiently your team can find products when it’s time to prepare an orderWhat the average staffing levels are within the warehouse
Optimize Your Logistics Operations With OptimoRoute
Managing the logistics of your supply chain is difficult—there are many moving pieces to keep track of. And this makes finding ways to lower your costs even more challenging. Fortunately, you don’t have to do all of the work by yourself. Using software like OptimoRoute alleviates the burden of manual logistics planning by streamlining the process. You can use the platform to facilitate essential logistics tasks, including:
- Planning routes up to five weeks a timeCreating efficient routes while
maintaining deadlinesTracking purchase orders and deliveriesSending delivery reminders and updates to customersCreating employee schedulesDriver manifest, load sequencingMobile app for driversGenerating reports on performance
OptimoRoute also lowers costs by using route optimization to reduce overall mileage. Reducing your mileage helps improve your bottom line by lowering your fuel costs. It also extends the life of your delivery vehicles by ensuring you’re only using them as much as you need to.
Start your không lấy phí, 30-day trial to see how OptimoRoute can help you improve your logistics processes and lower costs.
FAQs About Logistics Costs
In this section, we’ll address three of the most commonly asked questions about logistics costs.
What is the biggest logistic cost?
Delivery and transportation costs are the largest expense for logistics, with last mile delivery accounting for 50% of total shipping costs.
How do you calculate logistics costs?
Group your expenses into four categories: warehousing, transportation, labor, and equipment. Write down the exact cost of each expense in all four categories. Then, add up costs for each category. To calculate your overall logistics costs, add the costs of all four categories together.
Why is logistics so expensive?
Supply chains around the globe are facing shortages of materials, labor, and warehouse space. These shortages drive up prices, increasing logistics costs for supply chains in all industries.
Try OptimoRoute™ for Free
No installation or credit card required